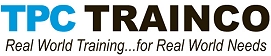 TPC Trainco
presents
Predictive Maintenance & Condition Monitoring On-Site Training
Learn how to develop a Predictive Maintenance program & monitor the results!
Course Description/Agenda
Purpose of Seminar:
With ever increasing demands from top management to do more work and decrease costs, investing in predictive maintenance and condition monitoring makes more sense today than ever. While many organizations still rely heavily on time based maintenance, it’s a proven fact that condition monitoring maintenance requires less personnel and saves money and downtime.
This course provides the fundamentals of PdM and condition monitoring applicable to plants, facilities and manufacturing lines. Predictive Maintenance & Condition Monitoring will provide students with a framework to make the right decisions on what equipment needs condition monitoring, what technologies to use to meet their needs and how to measure the effectiveness of their decisions. In addition to exposing students to the principles and options for a program, they will learn about real world applications that have benefited other successful maintenance programs.
By the end of this seminar, students will be able to go back to their facility and immediately apply what they learned to help make their maintenance process more efficient and less expensive. Training like this never costs – it pays! |  | Course Objectives: Upon completion of this course students will receive a personalized American Trainco Certificate of Completion and 1.4 CEU’s (Continuing Education Credits) approved by the Maintenance Training Association of the Americas indicating that he or she has learned how to:
Identify Why Time Based Maintenance Doesn’t WorkDescribe the Benefits of a PdM & Condition Monitoring ProgramIdentify What Equipment to MonitorUnderstand Different PdM TechnologiesPredict What Maintenance Needs to be done and WhenHow to Choose the right PdM Technologies for YouMeasure the Effectiveness of Maintenance DecisionsCommunicate the Condition Monitoring Program through the FacilityHow to Choose a PdM Service ProviderHow to Implement a PdM Program |  | Who should take this course:
This seminar is a must for anyone who is involved with maintenance at industrial plants, utilities or commercial and private building facilities. Attendees come from a wide variety of industries, skill-levels, company sizes, and job titles, so if you’re not sure you’ll fit in or will benefit from the class, don’t worry – you will! People who will benefit from attending this seminar include…
- Maintenance, Operations & Purchasing Managers & Personnel in:
- Manufacturing Plants
- Commercial Buildings
- Utilities
- Hospitals
- Waste Water Facilities
- Schools
- Government Buildings
- Shopping Centers
- Office & Apt Buildings
Including: - Maintenance Personnel
- Maintenance Managers
- Purchasing Agents
- Operations Managers
- Plant Managers
- Manufacturing Managers
- Production Managers
|  | What you will take home:
- American Trainco Seminar Manual - detailing all presentation material covered n the class
- Personalized Training Certificate with 1.4 American Trainco Continuing Education Units for attending this two-day seminar, approved by the Maintenance Training Association of the Americas
- All the information you need from asking our instructors specific questions about your own equipment or facility
|  | Course Outline / Agenda:
PdM or condition based maintenance attempts to evaluate the condition of equipment by performing periodic inspections while the equipment is still in service. The ultimate goal of PdM is to perform maintenance “just in time”, before the equipment fails in service. This two-day course is for maintenance personnel, operators and managers who desire to understand how condition monitoring can increase the efficiency of their maintenance program while reducing costs. This course will teach you what equipment to monitor, what technologies to monitor it with and how to measure your success. Students will gain an understanding of real world applications to help them implement a PdM program at their facility.
Predictive Maintenance Program Types Predictive Maintenance Program TypesBreak downPreventivePredictive
Failure Rate vs. Time Bathtub CurveDefinition: Weibull Distribution Curve of Failure Rate vs. Time
Sixteen PdM Program Benifits How to Develop a PdM Program Worksheet with Microsoft Excel
Four Foundations for Improving ReliabilityDeveloping and Fostering the Culture of ReliabilityProduct MissionReliability SpecificationsDefining Universal Failures
Comparing Maintenance Strategies based on Cost and Availability with “Large Truck Case History”Run to FailureScheduled Repair/ReplacementOn-Condition InspectionsCase History
Basic Concepts of FMEA (Failure Modes and Effects Analysis) and FMECA (Failure Modes and Effects with Cause Analysis) Ten Basic FMEA Steps
Techniques for Identifying Probability and Costs of Equipment Failure Recovering CMMS DataFMEA Data - Failure Modes and Effects AnalysisIEEE 493 Standards of Electric Motors
Using Maintenance Log Data Times-To-FailureSuspension TimeTimes-To-RepairMTBF - Mean Time Between Failures
Root Cause Analysis for Beginners What Happened? How? Why?How to do Cause Charting for Root Causes Possible CausesRecommendationsImplementation Action Steps
Interactive Excercise - 1.5 Hours
How to Sell Root Cause Analysis to Managment Preserving Evaluation DataBuilding the Analysis TeamAnalyzing the DataCommunication of Findings and RecommendationsTracking Cost SavingsCalculating Bottom Line ResultsCase History: How to Set Up a Seal Failure Analysis ProgramFour Step Process used by Predictive Maintenance Services Inc.
The Role of Reliability Centered Maintenance NASA’s Guiding Priciples of RCMFive RCM StrategiesReview of FMECAReview of RCFA-Root Cause Failure Analysis
PdM for Manufacturing Plant Operators
The Relationship between Availability and ReliabilityRelationship ChartProfit benifits of Operational AvailabilityHow to Calculate Up-ti
|
Add to favorites
Email this page
|
|